It is corrosion resistant, has a long lifetime, it is immune to electric interference, no electronics are required downhole, and the “cable” is only a quarter of a millimeter thick. Fibre optic sensing technology has a lot to go for. Yet, until a few years ago, its uptake in subsurface projects remained limited. How widespread is the use of fibre optic sensing technology now, and what is it primarily used for? And also, how easy is it to process the data and what is being done to make it easier? For the cover story of the current issue of the magazine, we spoke to several experts in the field to find out. In this online article, which is the first of three, Andrew Garioch from Well-SENSE discusses the use of fibre optic sensing technology in well interventions.
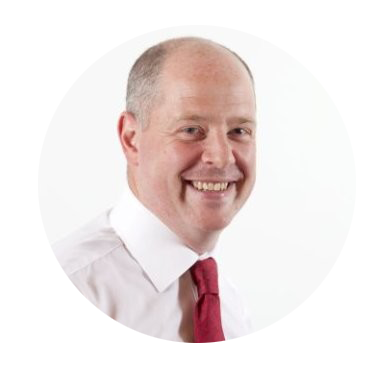
Fibre optic sensing using interventions
There may not always be a need for permanent installation of fibre optic cables, as existing tools sufficiently monitor production and pressure. In those cases, an intervention may be all that is required to obtain a dataset across that entire well path that would allow for immediate detection of leaks or identification of low-productivity reservoir zones.
Aberdeen-based company Well-SENSE have developed a methodology to effectively run well interventions using fibre optic technology. I visited operations manager Andrew Garioch at their facility to take a look in their workshop. It is surely a workshop, but it is nothing compared to the nuts and bolts nature of a conventional wireline tool workshop.
First of all, all the work is done in three mobile units that could be easily lifted and taken to any site in the world requiring their expertise. Secondly, nuts and bolts are quite rare because the tool is essentially an aluminium probe in which up to 30,000 feet of telecoms fibre optic cable is waiting to be unwound.
Deployment of the probe is also quite straightforward. It descends in the well through gravity. As an example, in a gas well it takes one minute and 30 seconds to reach TD at 3 kilometers depth. To push the tool in horizontal sections, pumping is the conventional methodology at the moment. “But we are working on a self-propelling mechanism that also takes away the need to do that”, says Andrew.
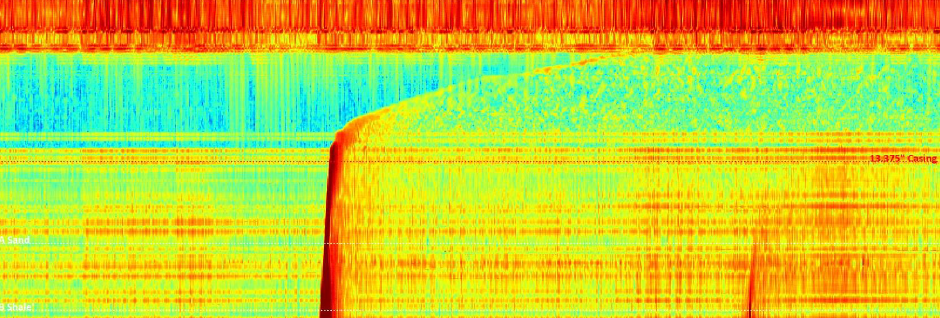
And what happens after data acquisition? “The aluminium probe will degrade in a matter of days, out of the way in the rat hole at the toe of the well”, says Andrew, “so there is no need to retrieve anything.”
We can usually report the results of the measurements back to the client in as little as an hour after deployment
But, what looks like a great advantage has also resulted in questions, particularly from people in HSE. “What if we will see the probe or fibre lift in the wellstream and compromising equipment?” is a question he sometimes gets. “My answer to that is twofold, says Andrew. “First of all, sand production is probably more “erosive” than the fibre left behind and if there is a concern about debris we can make the probe even more dissolvable, further reducing the risk.”
One example where interventions using fibre optics were really instrumental is when leaks occur as intermittent bursts after a phase of pressure build-up. “Conventional logging tools can easily miss such an event, but fibre optic sensing will always detect these, because of the full wellbore coverage provided by DFOS”, said Andrew. “And, we can usually report the results of the measurements back to the client in as little as an hour after deployment”, concludes Andrew.
“Our market is expanding significantly at the moment”, Andrew says. “We have recently had a lot of wins in Australia, and there are new opportunities in the mining sector. “The North Sea is a bit slower with reduced intervention activity and financial restraints associated with the windfall tax.”