It is corrosion resistant, has a long lifetime, no electronics are required downhole, and the “cable” is only a quarter of a millimeter thick. Fibre optic sensing technology has a lot to go for. Yet, until a few years ago, its uptake in subsurface projects remained limited. How widespread is the use of fibre optic sensing technology now, and what is it primarily used for? And also, how easy is it to process the data and what is being done to make it easier? For the cover story of the current issue of the magazine, we spoke to several experts in the field to find out. In this online article, which is the final of three, Chief Product Officer Garth Naldrett from Silixa discusses the use of fibre optic sensing technology in oil and gas and beyond.
A dissolvable tool – A conversation with Andrew Garioch from Well-SENSE
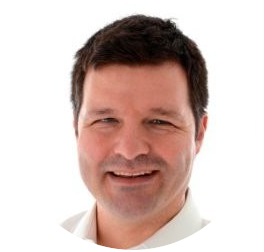
Not a new technology
“When you drill and complete a new subsea well these days, it is for sure that electrical temperature and pressure gauges are being installed”, says Garth. “Twenty-five years ago, it was a rarity for that to happen, but nowadays it is standard and accepted practice. Why am I saying this? Because I think that in 10 years, nobody would risk installing a subsea well without fibre optic sensing.”
Fibre optic sensing is not new. “My first encounter with fibre optic cable technology was in the late nineties at the ETAP field in the UK North Sea”, says Garth. “Given the high temperatures in the wells, people advocated for having fibre optic temperature and pressure gauges installed instead of electric ones. However, it turned out that the connectors were not as reliable as was hoped and electrical gauge reliability just developed faster during that time.” It then took about twenty years until the first Distributed Acoustic Sensing (DAS) was installed in a subsea setting.
This first goes to the BP Atlantis project in 2020. “But since then, we have done around 20 installations of DAS systems in subsea wells across the globe”, Garth emphasises. “Compared with the limited activity pre-Atlantis, it shows the growth the technology has seen over the past few years.”
“It doesn’t mean it is easy though”, emphasises Garth. “If you think the oil and gas industry is slow in taking up new tech, the subsea world can be even more of a challenge. To install fibre optic cables, we need a connection between the tubing hanger and the subsea tree. This is also one of the most important parts of subsea wells, forming the critical element of the pressure control system in the wellbore. So, doing anything that could affect the well’s reliability or integrity is being looked at very critically. As a solution, what we’ve been doing is retrofitting electrical connectors with fibre optic connectors, which works. However, in some fields that is not an option and the type of connector also varies significantly, so there is surely no plug-and-play here!”
Addressing a 3D imaging problem
On Atlantis, a deep-water development in folded Miocene strata, the reservoir was hard to image using conventional seismic data, because of the presence of salt above the productive interval. To map the reservoirs with more confidence during the third phase of development, permanent fibre was installed in a number of newly drilled wells. “The advantage of this is that any repeat surveys do not add a huge cost to the OPEX of the field, because the “geophones” are already installed in the wells”, says Garth. “And the repeat surveys are done anyway using ocean bottom nodes, so the additional data obtained through the fibre is essentially for free.”
Another advantage of fibre optic seismic acquisition is that the resolution of the data is better than using conventional geophone acquisition on the sea floor, because the acoustic signal is only travelling one way through the subsurface towards the receivers below. Using ocean bottom nodes or streamers, the signal needs to travel back. In that process, the higher frequencies get lost through attenuation, which leads to a loss of resolution compared to using DAS”, says Garth.
“It’s the ability to map reservoirs in a higher resolution and the low cost of repeat surveys that have been the driver behind the use of DAS in the Gulf of Mexico”, continues Garth. “We think that there is equally a lot of potential in the pre-salt play in Brazil for instance, as these reservoirs are experiencing the same imaging problems as we see in the GOM.”
“The value is at the back-end of the project” – CCS
In an oil or gas field, the most important changes in the field’s behaviour will be observed within the first three to four years from the onset of production. In contrast, in CCS the most critical phase in the lifetime of an injection project will be the tail end of the production cycle, as it is at these moments that integrity issues could start to play up, or plume behaviour may start to deviate from expectations. In addition, with any CCS project, there will be the requirement to keep on monitoring until after injection has ceased. That’s why the lifetime of sensors is more critical in a CCS project than in an oil and gas project. “And that’s where fibre optic sensing comes in, because the material’s lifespan is much longer than electrical sensors”, says Garth.
And it is not only the seismic mapping of plume migration that fibre optic sensing can help with, it is also the recording of strain – so induced seismic events – and temperature. Strain measurements in particular are a vital aspect of CCS monitoring, given that induced seismic events have occurred in a number of CCS injection projects. The Castor site in Spain is a well-known example, where seismicity was observed within days after the start of injection, and continued until after injection had stopped due to movement of the pressure front. “It reiterates the need to keep on monitoring after injection has ceased”, Garth says. “This year, we will be working with Perenco to monitor their injection trial in the Leman depleted gas field”, he says. “As such, it will also be the first case of CO2 injection into the UK North Sea.”
Seismic acquisition through DAS will unlikely replace OBN surveys though. Because receivers are by default fitted in the existing wells, the further away from them the weaker the signal will be. This is probably the reason why BP is also still acquiring OBN surveys in addition to the data gathered through DAS.
In the North Sea, seismic acquisition through DAS is not a big thing. “That’s because the environment is more benign to repeat conventional surveys”, explains Garth. Positioning is less of an issue without the loop currents that characterize the GOM, the water depth is much shallower, and the salt imaging problem is not so much of an issue with oil fields in the North Sea.”
Instead, Silixa has been busy installing fibre optic sensing in the Norwegian sector for production optimization. The best-known case is the massive Johan Sverdrup development, which has got its first generation of dry-tree development wells fitted with fiber optic cables as well as the subsequently drilled dry-tree wells. “It’s all done to ultimately reach a much higher recovery factor than conventional oil fields, plus the ability to identify integrity issues in the wells much quicker”, says Garth.
Ideal for machine learning
“If there is one subsurface technology that lends itself for data crunching using machine learning algorithms, it is the data that come out of DAS cables”, continues Garth. “The breadth of possibilities in DAS data is endless, as well as the size of the data stream. There is a lot of talk about digitalization”, he continues, “but you do need data to feed the algorithms.” Fibre optic sensing clearly provides this challenge, both in the data bandwidth as well as the rate of data generation realms.
In some cases, it is the rate at which data ins being generated that has even led to operators not using the data at all. One case of that particular issue is known to us, from a fairly new gas development in the North Sea. A representative of the company told us that the DAS data has not been used at all yet, because of a lack of expertise to process it.
“Our solution for this is called Edge Processing”, says Garth. “Rather than sending all the data to the cloud, we analyse it on the spot, right on the platform at the well head, and only transmit the data that have flagged something of interest.”
So, the capabilities are surely there. “I wouldn’t say it is complete, especially when it comes to standardization and integration with other types of data such as well logs, but there is certainly a solution in place that allows data to be rationalized.”
Reservoir section
If fibre optic cables are being used for seismic data acquisition or leak detection in the overburden, the cables don’t need to be run through the reservoir section. That is different from when the technology is to be used for inflow monitoring and detection of non-productive zones or water breakthrough. In that case, the cables need to be run across the reservoir section. However, that is not a trivial thing.
“It is the connection between the lower and upper completion, with the production packer as the barrier in between, that poses the challenge to get fibre into the reservoir section”, says Garth. There is no straightforward solution for that yet, especially on subsea wells, which is why there are several research groups at the moment working on that. “Once a technical solution has been found for this, I expect that the market opens up even more.”