It is corrosion resistant, has a long lifetime, no electronics are required downhole, and the “cable” is only a quarter of a millimeter thick. Fibre optic sensing technology has a lot to go for. Yet, until a few years ago, its uptake in subsurface projects remained limited. How widespread is the use of fibre optic sensing technology now, and what is it primarily used for? And also, how easy is it to process the data and what is being done to make it easier? For the cover story of the current issue of the magazine, we spoke to several experts in the field to find out. In this online article, which is the second of three, Andres Chavarria from Luna Innovations discusses the use of fibre optic sensing technology in oil and gas and beyond.
Andres is Luna’s Technical Director and a geophysicist by background. He worked with conventional seismic before making the move to fibre optic cable technologies about ten years ago. Since then, he’s shown to be a real advocate of the technology with multiple conferences and papers and posts about this regularly on LinkedIn. I caught up with him whilst he visited the UK.
See also: A dissolvable tool – A conversation with Andrew Garioch from Well-SENSE
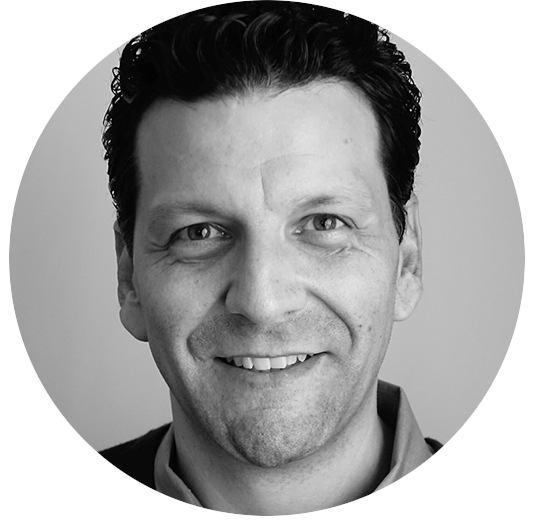
DAS and DTS
The main fibre optic sensors that are being used in oil and gas wells are DAS and DTS. “While Distributed Temperature Sensors (DTS) are quite straightforward in the sense that they record temperatures, Distributed Acoustic Sensors (DAS) measurements include seismic, acoustics, ultrasonic and even temperature”, explains Andres. “There is a wealth of signals that saturate these instruments. And it is that wealth of data that needs to be filtered properly to get to the right people.”
Permanent installation of fibre optic cables is increasingly being done in HPHT environments where conventional sensors are bulky and less reliable. In land wells, the fibre optic cables are often attached to the casing. In offshore wells, they are attached to the production tubing.
“It is the ability to take permanent measurements along the entire well path, rather than temperature and pressure gauges at a few locations along the well that form the real advantage of this technology”, says Andres. “For leak detection, fibre is critical, because usually within a few seconds we are able to say at which depth the leak occurs. Another advantage of fibre is that you don’t have any electronics in the well – it is a passive sensor with a very long operating life.”
And it is the long operating life and the simple design that has caused fibre optic sensing to appear on the radar for CO2 monitoring. With requirements to keep on monitoring CO2 plumes until long after injection has finished, there is an obvious niche for the technology.
But what is the expected lifetime of these fibre cables? “The oldest ones operating in the field are around 30 years old”, says Andres. But that was with the technology of that day. “I also know of cables fitted in steam-flood assisted oil production in SAGD and the Middle East, and these have been operating for at least 8 years already. I don’t know if they are very happy, but certainly, they have not degraded and continue doing their work.”
Data handling
With a single well being able to generate up to 2 Terabytes of data per day, how do you process the data? It is clearly one of the challenges the fibre optic monitoring industry is facing. “Believe me”, Andres says, “I know companies that have shared years of fibre optic sensing data with me that no one has looked at, because it has not been processed.”
“First of all, after a certain amount of time”, says Andres, “data may be deleted if the analysis has shown that nothing is wrong in the well.” But before that decision can be made, the data need to be analysed. “For that reason, we have focused on real-time processing in recent years, in order to get information on temperature, strain or acoustics to the relevant people in an operator. In a way, it comes down to the ability to spot the discrepancies in the data stream straight away and put a little alarm bell on them.”
But how long do you keep the data? “It depends on the project we work for, sometimes it is a couple of weeks, and sometimes it is a month’s worth of data”, Andres explains. Filtering the data is a great way of reducing the volume”, he continues. “For instance, once you know at which frequency you see the response from a gas lift valve, you can isolate these through frequency decomposition and save these as snippets of the entire recording. These snippets are much easier to handle and can therefore be kept as long as the field is in production.”
Geothermal
“In geothermal, we are involved with a whole array of projects, ranging from low-temperature to high-temperature operations”, says Andres. An interesting case is Enhanced Geothermal Systems (EGS) where stimulation of the reservoir takes place to generate a fracture network. Fibre optic sensing is used in these projects to monitor where these fractures are, which is exactly the technique for in the unconventional space in the US shale gas sector. “Using fibre optic sensing, we can illuminate the fractures, and see fluid communication from one well to the other. This provides a wealth of information on the performance of these systems”, Andres concludes.
Well abandonment
With a fibre cable having such a small footprint in a well, would it make sense to fit one in wells that are being plugged and abandoned permanently, such that monitoring can be done for leaks? “I know of a couple of cases where we did just that”, says Andres. “But really, these types of things should come from the regulator, as one can imagine operators may not be too keen on permanently monitoring a well for leaks once it has been abandoned according to the guidelines. “Saying that”, he adds, “there is sometimes a use for these cables in abandoned wells beyond leak detection. For instance, abandoned wells can be used for seismic monitoring.”
Another way of limiting the data that need to be processed or kept is decreasing the sampling rate. “An example is DAS, where thousands of light pulses are being generated every second, let’s say at 10 kHz”, says Andres. “Especially for leak detection, we don’t need to look at the data with such a frequency, and therefore down sampling takes place to up to a frequency of 0,01 Hz. It is what we call low-frequency DAS, and the result in a fraction of the size of the original datasets.”
“We have found that by far the best approach is to do this straight away at the data interrogator where the data come in, and process it in real time. First storing the data on a drive and then process it introduces another level of complexity that you’d really like to avoid.”
“Some companies have their own software and analytical tools to analyse the fibre optic data”, continues Andres. “We just supply the hardware and they do the rest. Others are lacking that expertise, and that’s where we can help with our analytical solutions. But even with the most experienced users, there will always be aspects to the data that need looking at in a more scientific way because it is not entirely clear what it means. At the end of the day, the technology is still fairly new and evolves rapidly, leading to more and more events to be detected – and more and more events to be then needing an explanation.”
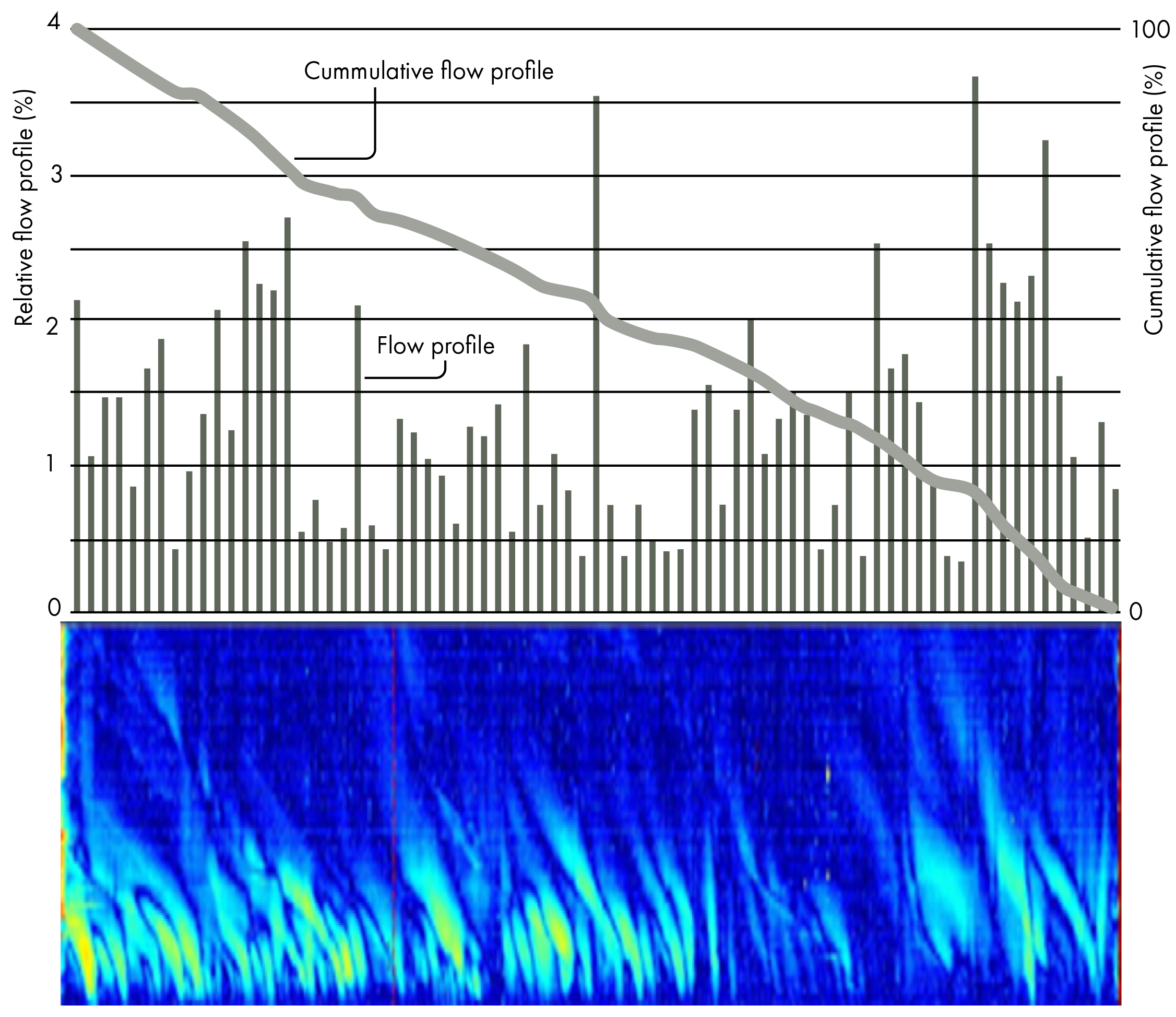
Various methods can subsequently be used to derive production profiles along the completed reservoir (above). Image supplied by Luna.
A new player
“The introduction of a new technology like fibre has not always been easy”, says Andres, “because of existing solutions already on the market. That’s why we have done a lot of flow loop work to make sure that the flow regimes that we can capture with fibre are representative of what the flow regimes in the well are. It is the same with seismic, where we had to use conventional geophones in combination with fibre to validate that you could get the same images of the reservoir.”
But as the technology has now matured, certain operators don’t require the validation phase anymore. Most of the service providers have also adopted the technology and made it part of their offering, which means that the technology is not being looked at as a disruptor anymore.
However, there is still a lot of R&D going into fibre optic sensing. For instance, research is carried out to identify different fluids. “On the hardware side, we are always improving things, such as reducing the costs of components and reducing the spatial footprint of the kit. One of the main things that we have seen a lot of progress in is the number of interrogators needed to receive and record the data. Now, multiple wells with fibre optics can be plugged in to the same interrogator, greatly reducing the operation’s footprint.”
The supplier landscape
Fibre optic cables are being deployed in many different environments, ranging from telecom to fire detection and in nuclear reactors. “The supplier landscape for the more conventional and widely used applications is very broad”, says Andres, “but when it comes to downhole use, the picture looks different. There are only a handful of companies that can provide the cables for these environments that can withstand the high temperatures and the carbon ingress that causes darkening. It really comes down to the engineering of the coating and the metal tube in which the fibre sits that make the difference in these cases, which obviously requires a lot of R&D.”