It is well known that elements such as copper, nickel and lithium are in high demand to provide materials needed for the energy transition. It is less well-known that chemical applications are equally required. For instance, offshore wind turbines need anti-corrosion chemicals to ensure a longer lease of life. Similarly, the geothermal sector needs chemicals to produce energy efficiently.
I caught up with David Halliday and Peter Wilkie from Roemex to hear how their company has found a niche in the geothermal sector and how they are expanding the service in Europe. Roemex has been providing production chemistry services to the oil and gas industry for nearly forty years, but their move into the geothermal sector, delivering solutions for scale and corrosion, is relatively new.
In early 2019, the company was already working on the development of scale and corrosion inhibitors for the geothermal sector for about two years, but it took time to get traction.
“It took a declining injection well in the Netherlands in 2019 that formed the key moment for us”, David recalls. Roemex was called for help. “We fixed the problem, injection could restart, and the client was happy”, said David. The Aberdeen-based company is now involved with more than 10 geothermal projects in the Netherlands, where it assists with corrosion and scale mitigation.
We have seen projects in close proximity to each other where one required scale and corrosion inhibitors quickly, while the other one did not.
No two brines are the same
“Rather than relying on products taken from our portfolio used in the oil field, we saw early on that the geothermal sector required another product type”, David explains. “The main reason for that”, as Peter filled in, “is the fact that oilfield inhibitors used in predominately water systems (brines) do not have the same behaviour as they do when in a hydrocarbon environment.”
“Formation water can be corrosive”, says Peter, “especially because of the CO2 dissolved in the brines.” Combined with flow rates that are seven to eight times as high as in an average oil well, it is no surprise to see that the materials in a geothermal doublet are put to test from day one and that only the highest-spec materials can withstand corrosion.
“However, it is too simple to state that every geothermal project needs the same level of support”, David adds. “We have seen projects in close proximity to each other where one required scale and corrosion inhibitors quickly, while the other one did not”, Peter explains.
Lab testing
To provide a tailored service and minimise the amount of chemicals required, the company performs laboratory tests on site in Aberdeen where different brines can be tested against different concentrations of chemicals. The laboratory is part of a project in collaboration with the University of Leeds where, under the umbrella of a Knowledge Transfer Project through Innovate UK, research is carried out on scale and corrosion prevention, both at surface and under subsurface conditions.
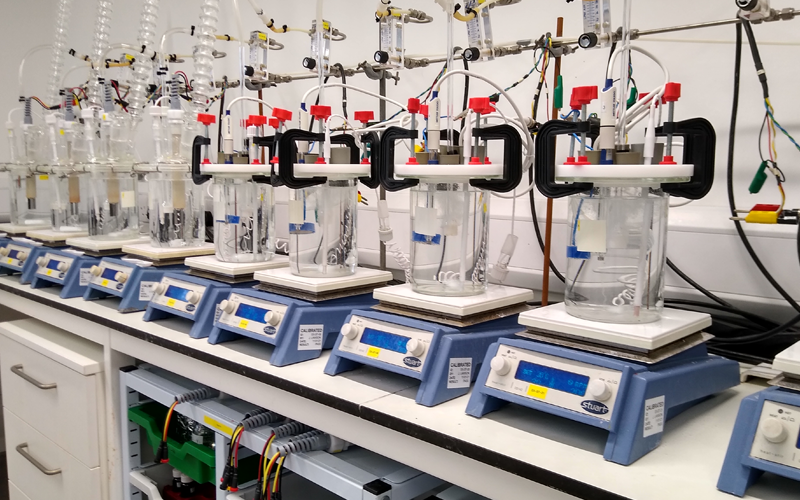
Marco Castillo, who is heading R&D in Geothermal corrosion inhibitors, shows a graph that illustrates how a stop in the supply of corrosion inhibitors does not result in a sudden and rapid increase in corrosion rates. “Even after supply was terminated”, he says, “the surface is still protected for a while and will only see a gradual increase in corrosion rate. This highlights the persistency of effective corrosion inhibitors and is key in high flow environments.
The geology matters
“Looking at the different aquifers in the Netherlands from which geothermal energy production takes place, the Rotliegend brines are the ones that poses the biggest challenges because of their mineral content”, David further illustrates. “Issues related to precipitation of lead in either the well or the heat exchanger is something that we particularly see in some Rotliegend aquifers”, adds Peter.
It seems likely that the surrounding geology is responsible for the composition of the brines in reservoir; the Rotliegend in the Netherlands is overlain by the Zechstein Kupferschiefer in many places, which is a well-known black shale that is characteristic of its metal content.
Expanding into Germany and France
The company is now actively trying to expand into other regions in Europe. “We have just come back from a conference in Offenburg, where we spoke to local operators who were forthcoming with very practical issues that they are dealing with on a daily basis”, David says.
Each area where geothermal energy production takes place will require a different approach though. “In the Munich area in Southern Germany, water production takes place from a reservoir that is considered an aquifer for drinking water, so that puts a very stringent set of rules in place”, David adds as an example.
The company hopes to perform a trial in the Paris area later this year, another geothermal hotspot that has been operating for many years. “We think that we can make a difference here, because we have focused so much on making our products more sustainable”, David says.
It takes time to develop bespoke chemistry, time to undertake performance and compatibility testing. More crucially, it takes time to establish relationships & build trust, admits David. For the team at Roemex, that time is invested, and that’s what doing business is all about