“I have always wanted to have one foot in the field and one foot in the lab, to better solve practical problems in the oilfield”, says Guy Wheater on a few occasions during our conversation.
Guy works for GAIA Earth Technologies, where he invented and developed their cable protection system. At its core, it is a seemingly simple tool called a wireline standoff that prevents cables from sticking in wellbores during wireline logging operations.
See here for a short technical outline of the main causes for cable sticking and what can be done to prevent it.
It took many years of development and thousands of hours of hands-on labour and field trials before it got to the stage where it is now: a market leader for a niche product that is used by 25 oil and gas companies internationally.
Here, we tell the story of how Guy got the idea of developing the cable protection system and the business activities that spinned off from it. It is a story of having a vision, keeping things in your own hands and gaining the trust of customers. But before we dive into how Guy got to the idea to develop this standoff tool, let’s take a look at his formative years first.
Wannabe engineer
“I grew up on a farm in Yorkshire, gaining many skills and lessons from my father; by my early teens I was a competent welder, I could lay concrete and sink a straight line of telegraph poles for a fence. My father managed to plant a deep will to succeed in me”, says Guy. “Secondary school was a distraction from my apprenticeship; lessons were tedious and felt irrelevant to me. Without much consideration, I drifted into Sixth Form, which was an even bigger academic challenge; I left there with D & E grades at A-level, but with a growing desire to become an engineer. I was generously offered a place at Coventry Polytechnic for a Bachelor degree in Engineering Studies – my only offer, unsurprisingly, with such dismal grades!
I threw myself into it, consistently studying up to 18 hours a day. Summers were spent in Yorkshire, picking potatoes during the day and working in bars at night – money was always tight. Three years later, just after turning 21, I walked into Cambridge University to start a PhD in mechanical engineering. I was an unlikely candidate but I was offered great support and encouragement by my tutor Professor K.N.C Bray and my peers.”
Cambridge changed Guy’s life and perspectives in many ways. “I met so many stunning individuals and had conversations that made me giddy; the people there had so many new and interesting ways of looking at things.”
A wooden spoon
“Early on in my research on turbulent diffusion flame structures, I was invited to a fluid mechanics seminar. A visiting scholar from the US showed his incredible lab facilities during a slide show and for a moment I thought I might be in the wrong place. Until someone at the back shouted out: “What is it all for?” It was quite a provocative question – the professor was taken aback and muttered “model validation.” The physicist had made his point.”
“Then, a rather scruffy guy came on stage, contrasting heavily with the person we just saw”, continues Guy. “He talked about vortex-object interaction, which is of value to many industry sectors. After presenting a series of complex equations on an overhead projector, he picked up a wooden spoon and whipped up a water vortex in a circular glass tank. He dropped in a small stick, and just as he had described mathematically, it tumbled erratically and then damped down. There was applause, the physicists approved!”
“In so many cases, one does not need expensive kit to do real science and penetrate the physics of things.”
“It amazed me”, Guy says, “and until this day, I hold that experience close to my heart. I was in the right place after all. In so many cases, one does not need expensive kit to do real science and penetrate the physics of things.”
Years in the field
Before he embarked on the challenge to develop the standoff tool though, Guy first spent about 10 years with Schlumberger. “I was told that they drive around Libya in Land-rovers and make a lot of money, which sounded rather appealing!”, he laughs.
Guy visited their research centre in Cambridge and they offered him a job in the fluid mechanics department. “After 6 months, appreciating my practical approach, they suggested me to go into the field for a couple of years, to bring that experience back into the lab. I joined the field after attending wireline training school and I soon realised there was no going back – wireline was a full-on adventure that I had a huge appetite for.”
Guy worked offshore and UK onshore for 2 ½ years, followed by remote desert locations for another 6 years in Oman and Yemen, then to Tanzania and back to Oman as a base manager.
“Being in the field makes you appreciate not only the nuts and bolts of operations, but also the significant challenges that may come with the environment”, says Guy. “It was a rich and addictive experience, from 250-hour logging operations with minimal sleep to dealing with security situations in Yemen. I watched the sun come up in the desert so many times, huddled with my crew, all of us filthy and exhausted, wondering how the hell we would get through the next 24 hours. But there was no place I would have rather been; physical challenges bind people together like nothing else.”
Special project
“In 1999, I was coming to the end of my assignment as the base manager in South Oman”, says Guy. “I heard I was going to be offered a special project by the brass in Schlumberger. The advice given was: “You can’t say no.” They wanted me to join a start-up business in Edinburgh, to market Scottish distance learning programs, and to help establish a Petroleum University overseas.
On paper, it was a great opportunity: to develop new skills whilst creating important access channels for U.K. Petroleum Engineering courses in Iran, India, U.A.E and Malaysia. However, I was fundamentally unsuited to the role, I did not like the people involved, nor did I see it as a win to remove my coveralls. For 3 years I faced serial difficulties but I completed the project as tasked.
Guy returned to his box apartment in London for nine months and pondered his future. “The main question was how to become the old me again?”, he says. “One day, I got an unexpected phone call from an old colleague with whom I’d worked in Yemen, asking if I knew someone who could go to Algeria to supervise a wireline logging job. The role was offered to me by Stuart Huyton, the founder of Gaia Earth Group. Stuart’s decency was immediate and authentic. He gave me purpose, a long-missed sense of belonging, and great optimism for the future. After what seemed like an interminable drought, the thunder had clapped and the bounce was back in my stride.”
“During that week in Algeria, I realised so many things: I had missed the action so much, the desert was a comforting déja-vu and I felt useful again – all of it made me really happy. It took four months before another job came along, and it was a hard wait, but I knew I had made the right choice.
Now, I could help build a new company, define our own culture and become the engineer I always wanted to be: something was going to be “Made in Great Britain” – but I did not yet know what it was going to be.”
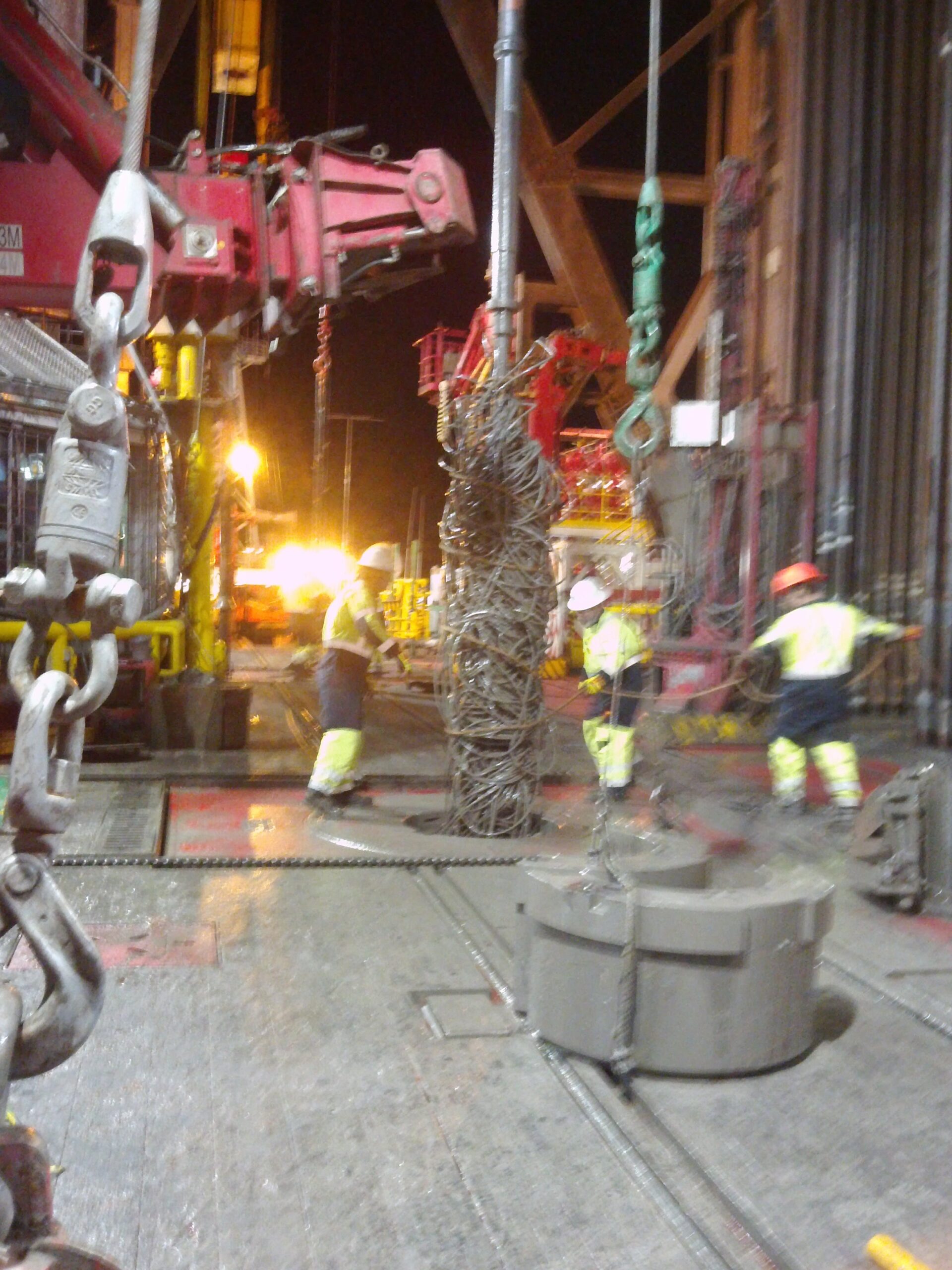
“Those wireline standoffs, I need them”
During the first decade with Gaia, Guy mainly worked on job planning and wellsite supervision projects all over the world. “In 2006, I did a fair bit of work on the Buzzard field in the North Sea, where we experienced repeated cable sticking during wireline logging operations”, he continues. “And then I realised, what am I going to tell the operator – Nexen? We don’t know why it’s happening and we don’t when it’s going to happen again and the only solution is to pull and hope. We loggers should be able to do much better than that!”
Nexen were positive to Guy’s initial suggestion to work on a solution to this problem and even offered some funding. Guy refused that, he already had a “wooden spoon” in the works – nothing more was needed at that stage.
In the meantime, he moved to Dubai for Gaia in 2007, where he found a machine shop able to build a prototype wireline standoff. “I took an amateurish picture of it on my balcony and sent it to Nexen. The photo of the prototype made its way to a few desks within the organisation until it ended up with Nexen’s drilling manager in the Gulf of Mexico. He called me at 11 PM one night, saying: “Hey Guy, those wireline standoffs, I need them.”
The first trials
Within thirty days of hard work in the workshop, Guy managed to produce the kit needed for the Gulf of Mexico job. “We ran the standoffs in a well with two sidetracks, where the main hole had experienced cable fishing. The standoffs eliminated all signs of sticking, even though the same wireline tool, mud, formation and overbalance were used. It was an early indication we might have a promising solution.” Field trials carried on for the next five years with continued success, leading to the establishment of Gaia Earth Technologies in 2016 as a spin-off to Gaia Earth Sciences – now forming Gaia Earth Group.
“I watched the sun come up in the desert so many times, huddled with my crew, all of us filthy and exhausted… But there was no place I would have rather been; physical challenges bind people together like nothing else.”
Another business opportunity
The success of the standoffs quickly led to another business opportunity. “Clients appreciate our standoff technologies”, emphasises Guy, “but they were even more interested in engineering due diligence for well planning, i.e. what are the sticking risks on my next logging job and do I need an intervention with wireline standoffs? That is always the question that needs answering.”
This made Guy aware that a software package was required to simulate well design and make a sticking risk assessment. This led to the development of Wire-pro, a tension and sticking package and a geological benchmarking framework, employing statistical data from global sticky wells. As such, Gaia’s Cable Protection System was born (GCPS), a synthesis of hardware, software, and wireline operations expertise. Since then, GCPS has seen ~ 30% annual growth in activity worldwide.
Building Wire-pro was all done using the money made through the standoff deployments. It made Guy even more convinced of the decision to create the software from scratch rather than trying to improve an already existing package on the market. “When you control the code, you can explore the physics and truly innovate – extracting the practical risk metrics that really matter”, he says.
The difficulty of gaining access
Thanks to GCPS, Gaia has now delivered many hundreds of wireline conveyance and sticking risk assessments, resulting in > 400 deployments and > 16,500 standoffs in the hole, with 99% efficacy. But even though GCPS is highly effective in predicting and mitigating cable sticking, many companies continue to clock up sticking-related NPT during their wireline operations. Why is that?
“On the service provider side, we are not yet included in their logging menus or standard workflows”, Guy says. “Cable sticking risk may not be assessed at the planning stage of a logging operation in some wells. This lack of oversight can be a colossal mistake.”
“On the client side, it can be difficult for a small business to gain access to the right people within an organization, unless you already know somebody on the inside. There are traditional methods of communication, such as websites, SPE papers and conferences, but nothing beats sitting around a table with a client and letting the conversation flow in the direction they deem necessary. Their perspectives, concerns and challenges drive the direction of our future R&D, which goes far beyond cable sticking mitigation.
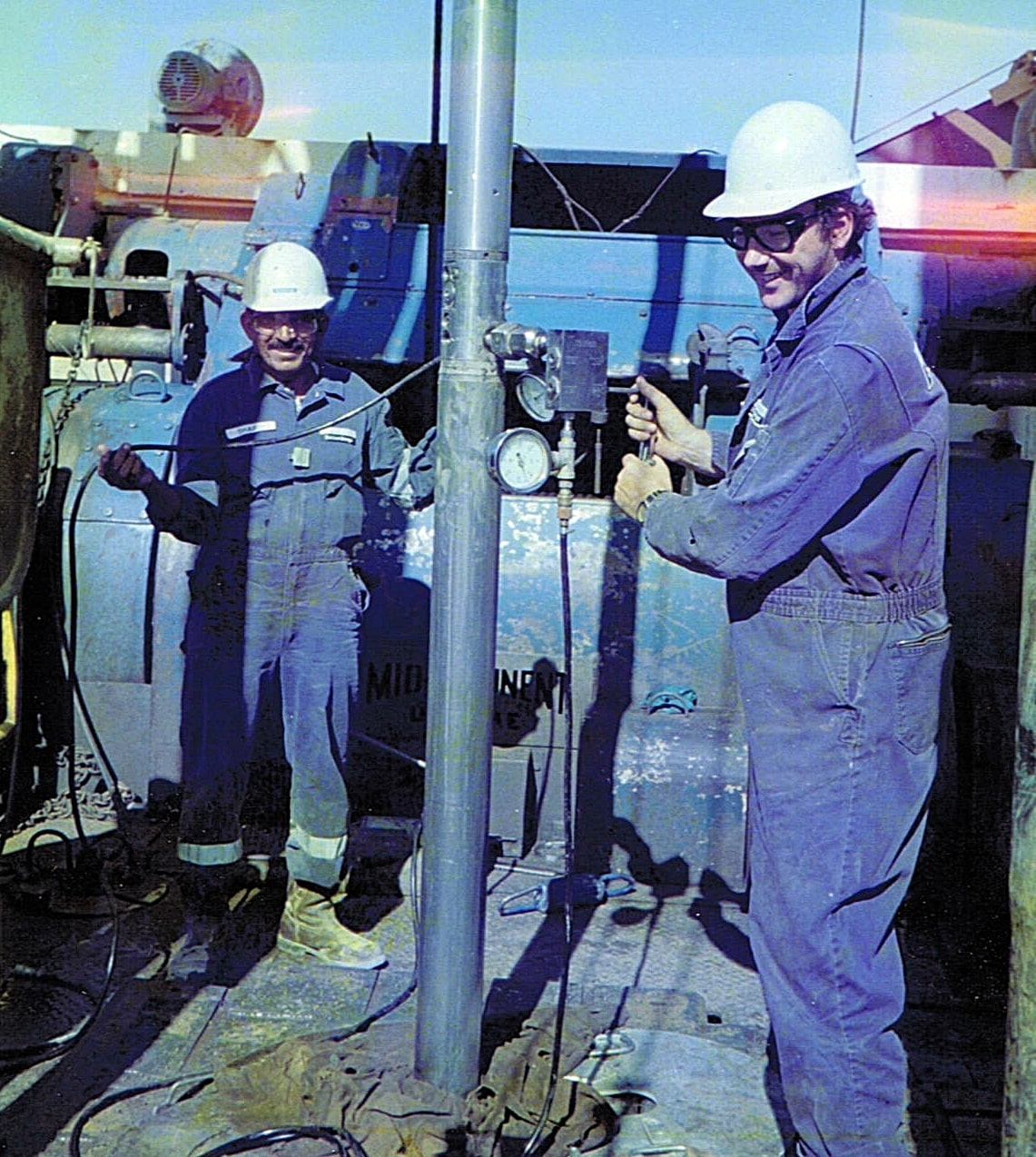
“Without the American support we would have no business to speak of, no active R&D and no investment in UK manufacturing.”
Put the money where your mouth is
The Gulf of Mexico is the basin that has seen the most widespread uptake of Guy’s inventions. Is that a coincidence? “Two words are enough to describe that”, says Guy: “Can do!” Americans love innovation, and love saving money. They are practical people who ask the right questions and are very open to new ideas and methods. I wish Europeans would be more American; dynamic, demanding, unashamed of making-hole and bringing the best tech to the table. Without the American support we would have no business to speak of, no active R&D and no investment in U.K. manufacturing.”
“I had never thought that the people in Houston would be so receptive to tools made by a Brit in his spare room in Dubai. But somehow the guys trusted me and were ready to put money on the table after a 30-minute phone call. It is something that I will always be grateful for, and it is something the world can take a lesson from.”
And as Gaia works on expanding their technologies and services portfolio, growing their business globally, Guy concludes: “You don’t need an expensive lab to do great R&D – any rig will do. What you need is curiosity and tenacity, a love of creativity and problem-solving – and maybe a $3 wooden spoon!”