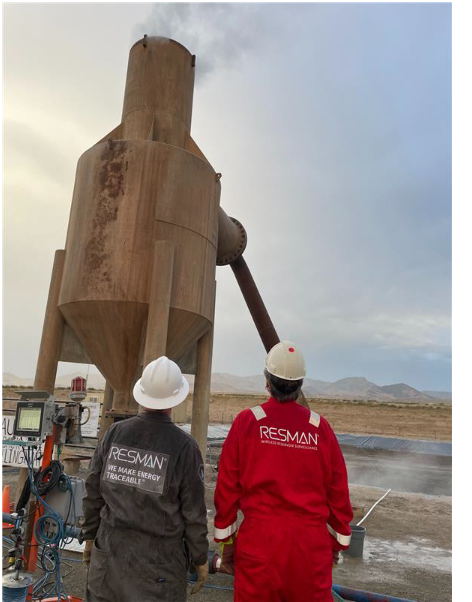
“The conventional oil and gas industry has been familiar with tracer technology for a long time,” says Roy Greig from RESMAN Energy Technology. “There, it is mostly used to determine which injector “talks” to which producer, calculate sweep area and direction, and more recently to calculate remaining oil saturation as fields mature.”
The temperature ranges in conventional oil and gas operations are relatively moderate compared to the extreme conditions encountered in some geothermal projects, particularly in volcanic regions. “For that reason, tracers developed for oil and gas cannot simply be applied in geothermal projects,” explains Roy. “This is especially true because we use organic compounds that tend to break down at higher temperatures.”
Yet, there is a growing drive from the geothermal industry to develop more robust tracers as their projects benefit a lot from knowing when and where injected water breaks through. This is especially true given that the alternative to organic tracers – using deuterium – is increasingly being scrutinized in many places around the world.
“The solution we came up with is two-fold,” says Roy. “First of all, we invested in lowering the detection limit of our machines that measure fluid samples returning from the field. While most tracer labs measure as low as parts per billion, we’ve pushed this down to parts per quadrillion. Because of this, we have been able to detect tracers in geothermal projects that were previously thought to be ineffective because they went undetected, leaving field operators confused and without data,” says Roy. “So, the significant investment into R&D and even more sensitive methodologies has proven to be successful.”
UTAH FORGE
“The Utah Forge project has been a key project for us,” says Roy. “Not so much because of the temperatures involved relative to some conventional geothermal plays, but because it’s given us the opportunity to validate new tracers for EGS (Enhanced Geothermal Systems). By understanding how injected fluid flows from the injection well, through stimulated pathways, and ‘hits’ the producer well, we can start to quantify the success of multiple unique stages relative to each other. The limited number of previously qualified tracers did not meet the requirements to characterize all unique stages in larger projects.”
“But that still requires us to develop new tracers that can withstand temperatures above 300° C,” continues Roy. “The main challenge was the limited number of variants at the industry’s disposal, especially for more complex projects. A series of different unique tracers that can be injected at fixed time intervals are required to achieve multiple datasets across the reservoir. As long as each tracer has a slightly different composition, there is no need to wait for one to be completely flushed before injecting the next one. That’s why raising the minimum number is essential,” concludes Roy. “And that’s also why we’ve invested in developing a broader range of tracers that can withstand the high temperatures used in some of our upcoming and current projects.”