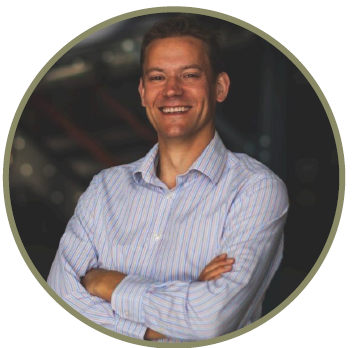
“If you don’t include the subsurface in the journey towards reducing CO2 emissions, it will be impossible to reach net zero”, says Frank van Bergen. Frank heads up the Rijswijk Centre for Sustainable Geo-energy (RCSG), where a broad range of facilities enable the testing of subsurface drilling technology for the energy transition.
“We know that drilling for geothermal energy production or storing CO2 in the subsurface requires a vastly different approach to material selection and technology”, says Frank. “Then, we also know that renewables are more cash-constrained than oil and gas, which puts even more emphasis on costs.”
This means that innovation in drilling technology is required to bring down these costs whilst maintaining high-spec material properties at the same time. “That is what we aim to do here in Rijswijk”, says Frank. “We play a facilitatory role in the development of new technology such that the full-scale implementation in the field runs as smoothly as possible. At the RCSG, new technology can be tested at downhole conditions and at a 1:1 scale.”
SMALL PARTICLES
When it comes to drilling faster, Dutch start-up Canopus developed a new drilling technology that bombards the formation with a continuous flow of small steel particles through a nozzle, thereby weakening the rock before the bit removes it. Prior to testing this technology in Switzerland, the RCSG facilitated a range of experiments whereby the initial design could be fine-tuned. The company is now embarking on experiments using a larger bit, and tests have already shown that conventional ROPs can be beaten by a factor of 2.5.
Drilling more than twice as fast
“When Shell decided it was time for another player to continue managing this extensive oil and gas drilling test facility, we saw it as an opportunity to give it another lease of life with the energy transition in mind”, continues Frank. “In doing so”, he says, “we target the higher TRL levels of product maturation, just before piloting the new solution in the field. Performing tests in a fully controlled environment may point out issues that might either jeopardize field implementation or severely delay it.”
“We have the means to test drill bits, downhole tools and other equipment and expose the material to different pressure and fluid regimes. We have a 380 m deep borehole that can serve as a real subsurface laboratory in which we can test the performance of tools and materials that are used for drilling, monitoring and operations, by replicating the conditions as closely as possible, which makes this a unique place.”
Let’s now look at a few examples of studies the RCSG has recently been involved with, further demonstrating the niche position of the facility.
We offer a fully scaled environment for testing conditions such as found in the subsurface
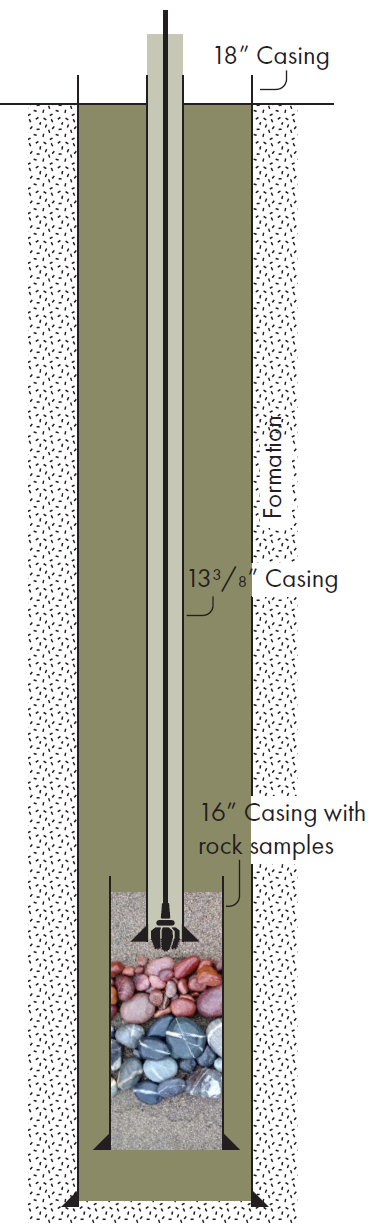
Temperature cyclicity
One of the differences between oil and gas wells and CO2 injection wells is the cyclicity in bottom-hole temperatures. Where oil and gas wells do not tend to experience large temperature variations at depth, this is very different in CO2 injection projects in depleted gas fields where super-critical CO2 expands as soon as it hits the formation, leading to a large cooling effect. This could in theory have a detrimental effect on the integrity of the cement between the casing and the bedrock, potentially leading to micro-fractures and the risk of CO2 migrating upwards through the annuli. Geothermal wells can experience similar thermal stress. Whether this damage actually occurs can be tested under controlled conditions in the lab. “The effect of these temperature changes on the integrity of wellbore cement can be simulated in the RSCG lab, at representative bottom-hole temperatures”, says Frank. “We are running a project along these lines at the moment.”
Loops and grout
The drilling of shallow geothermal closed loops has seen a dramatic increase over the past few years, in response to rocketing gas prices and government incentives to decouple domestic heating from the gas grid. The depth limits of these closed loops are now shifting from a “conventional” 200 m to being closer to 500 m, all with the drive to extract more energy and potentially provide blocks of houses with baseload energy instead of having one loop per house.
The boreholes drilled for these loops are filled with grout, a mixture of cement and clay, to prevent any cross-flow. “We are now looking at how these grout mixtures behave when exposed to higher pressures and potentially larger temperature variations”, says Frank. “The thing is, due to extraction of energy from the circulating fluids by the heat pump, temperatures in the borehole can drop close to freezing. We are currently running a project that monitors permeability changes of the grout under those circumstances, which will enable us to provide recommendations with regards to the best cement-clay mixture.”
How to ensure hole stability?
In the Netherlands and many other sedimentary basins across the world, there is an increasing interest in exploring reservoir sands at relatively shallow depths (800 – 1,500 m) for open-loop geothermal systems that can be directly used for low-temperature heat grids or as input for heat pumps.
The clear advantage of tapping into reservoirs at this depth range is the likelihood of finding much better reservoir quality than when going deeper, which also takes away an important risk element in these projects. However, in return for better reservoir quality, lower formation water temperatures in the region of 30-50° C are commonly encountered. In turn, higher extraction rates are often required in order to produce similar amounts of energy compared to the deeper systems.
BENTONITE – NOT ONLY FOR DRILLING MUD
Another clear example of the critical role the facility played in the development of new technology is the work performed to test the role of bentonite as an agent to abandon wells rather than using cement. This originated as an idea but led to a full-scale testing project at the RCSG that ultimately culminated in a pilot in an existing oil and gas well. “The point where we are now — technical readiness for commercial deployment — would not have existed without the role the RCSG played in the process”, says Frank.
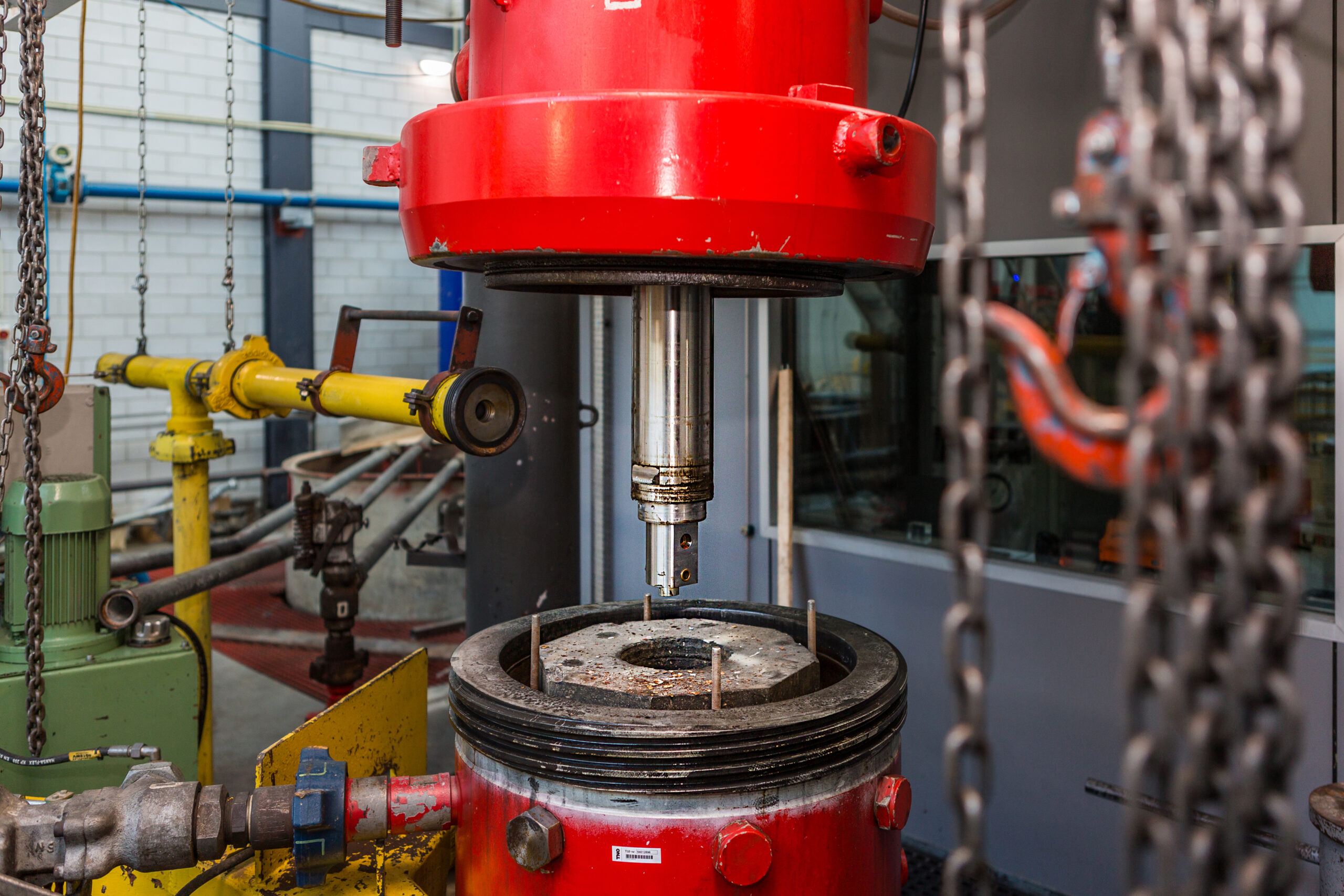
“At our center”, explains Frank, “we look into this from various angles. First of all, drilling rigs are an issue. Groundwater drillers are not allowed to drill beyond depths of 500 m because they don’t have the right safety measures in place, whilst an oil / gas rig is too expensive to use for holes of this kind. We are looking at ways to make it possible to have the best of both options – the agility and affordable running costs of groundwater drilling rigs and the safety features of more powerful oil and gas drilling installations.”
If you don’t de-risk new technology properly in the lab, full-scale field implementation can be a very costly and frustrating exercise
“Secondly, we are looking at ways to optimize circulation in horizontal wells that are to be drilled in these poorly consolidated sands. Circulating too much may lead to wash-outs, but circulating too little leaves the cuttings in the hole. There is a narrow operational window here”, says Frank, “and we clearly need to test this to find out what the best operational procedure is.”
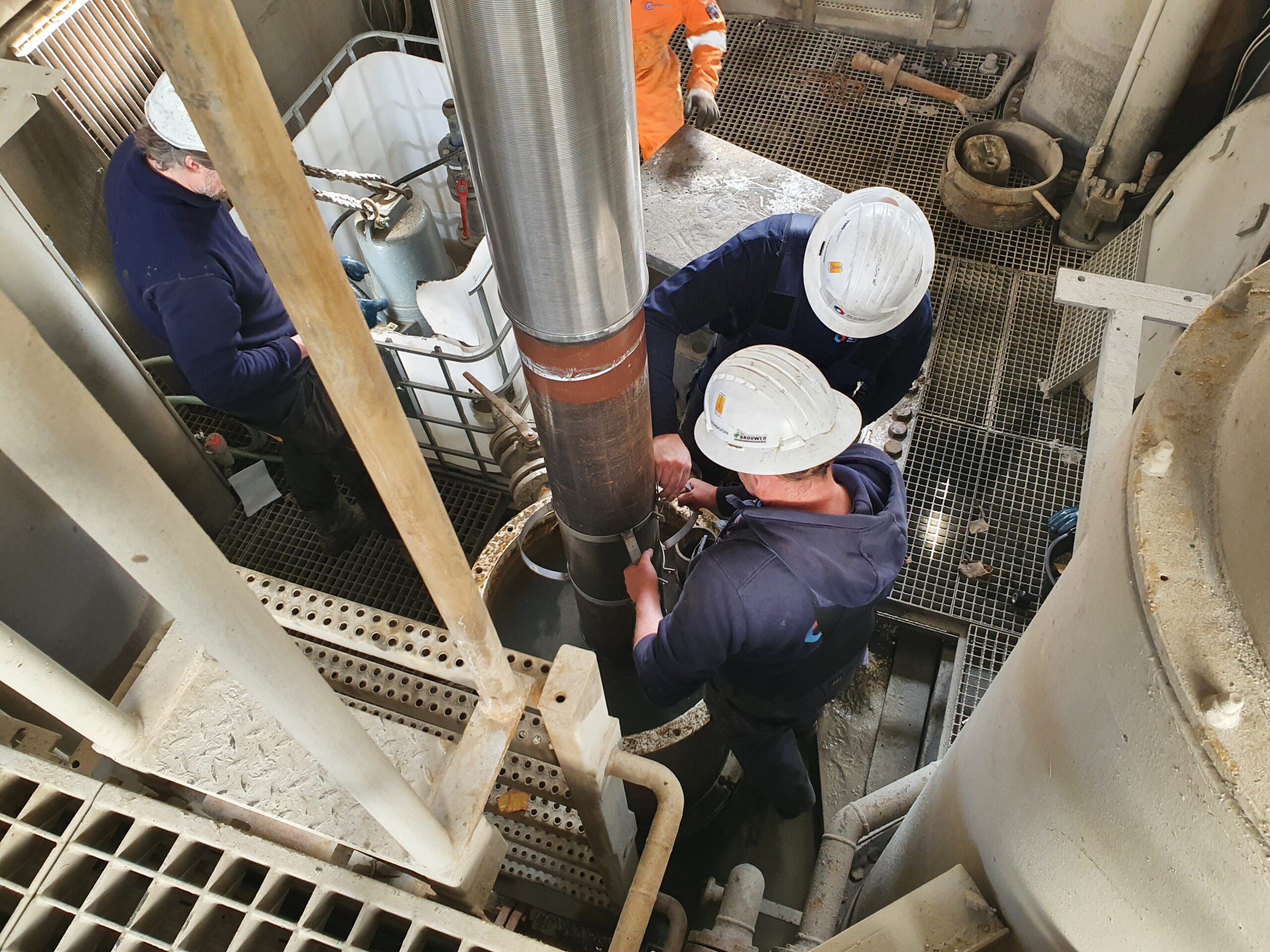
Working together
After five years of getting projects and technologies closer to maturation, it can be concluded that the RCSG has cemented its role in the development and demonstration arena. “We are here to help the implementation of subsurface projects in the energy transition. One thing that we are now particularly keen on”, concludes Frank, “is to start collaborating more with oil and gas companies that are looking to branch out into the geothermal or the subsurface storage space, and how our center can be used as part of the process that is often required to progress drilling technology towards successful implementation in the field. We welcome any companies interested in this to get in touch with us.”