Whether or not an oil or gas development makes money is highly dependent on the oil or gas price. If the price is favourable, an oil or gas project can generate significant profits. In the geothermal energy sector, such kind of speculation does not exist, as the price for energy is much less prone to fluctuation than oil and gas. Geothermal heat has to be used directly at source and cannot be traded or temporarily stored. It is a utility, not a commodity.
In addition, the investing organisations embarking on geothermal energy projects are less cash-rich than the bigger oil and gas operators. At first glance, this may suggest that CAPEX should be kept to a bare minimum. However, learnings from a first generation of geothermal systems drilled to depths of 2-3 km in the Netherlands and Denmark clearly indicate that integrity of the wells is key and therefore requires a relatively large upfront investment. This is to ensure that a geothermal system is able to run sufficiently long to achieve long-term return on investment.
Geothermal energy as utility is achieved by low OPEX, a high coefficient of power, a rigorous focus on quality and well integrity. For the initial project sequence this is 35m3/hr with 1,5 MWth power, an energy coefficient of 25 and price of €5/GJ. Dutch household heat-price is € 28/GJ with natural gas.
Corrosion
As a letter from the Dutch State Supervision of Mines in June 2020 clearly illustrates, an inspection of 38 geothermal wells in the Netherlands found that the tubing thickness had decreased significantly in 6 wells, whilst in another 15 wells a decrease of around 25% had been observed. Three wells had even leaked and were subsequently taken out of production.
These data clearly illustrate the challenges geothermal energy production from 2-3 km depth face; brines are corrosive, require high quality materials to withstand it and flowrates are high, causing erosion.
The situation in the Netherlands is not unique; two out of three geothermal systems drilled in Denmark had to be closed down because of technical issues, either because of salt precipitation in the pipes or corrosion.
A different way of designing geothermal systems
Being all too well aware of the problems facing the first generation of geothermal systems, Andre Mol from “Geothermie Groep Nederland” initiated a project to completely overhaul and rethink the way geothermal systems are being designed and implemented.
He argues: “Rather than trying to maximise flow rates from a reservoir as deep as possible, we aim to utilise all suitable and less saline aquifers for direct use. In addition, the system is designed in such a way that flow rates are well below critical velocity in order to ensure well integrity. The premium casing materials together with low operating pressures ensure a life span that enables the operator to run the system with minimal OPEX and maximum power efficiency. Unforeseen costs can be prevented by design and need to be ruled out in the cash-constrained utility market.”
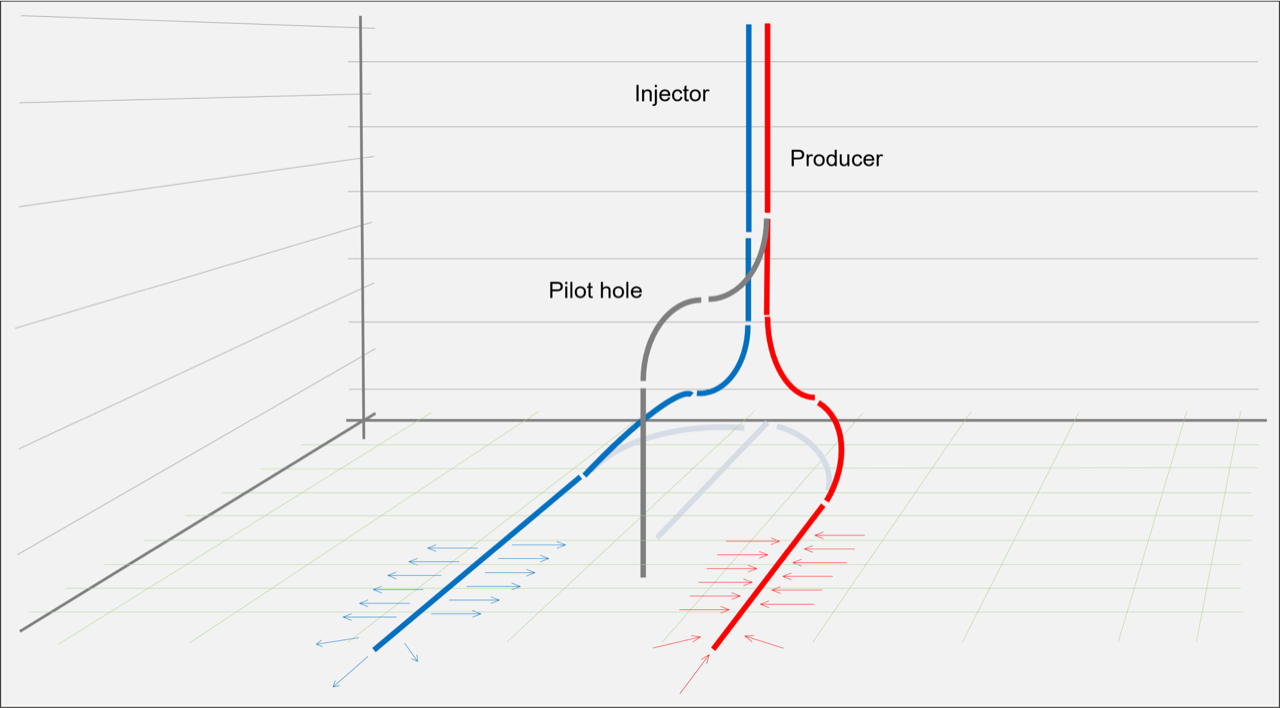
Treat reservoir as the client
“In order to design an optimal geothermal system for each location”, Andre adds, “we have to treat the aquifer as the client whom we need to build the system around.” In order to achieve this, he proposes to drill a simple pilot hole into the targeted reservoir first to obtain in-situ characteristics such as deliverability, which then allows the design to be completely tailored to what the subsurface is capable of delivering. “This is mainly to safeguard the total investment, preventing situations like in The Hague where a full spec system was implemented into the Triassic only to find out that the interval was problematic.”
HENK KOMBRINK