While there is a strong push towards replacing fossil fuels with renewable energy in areas like electricity generation and personal transport, some industry sectors remain ‘difficult to decarbonise’, such as cement manufacture and aviation fuel (see GEO ExPro Vol. 19, No. 2). CO2 is one of few alternatives to fossil fuels as a source of carbon and CCUS will be a vital component in making these ‘difficult’ processes greener.
Carbon dioxide has been captured at the point of emission and then reused for many years, primarily in enhanced oil recovery and in the production of fertilisers. Annual global consumption of CO2 was reported by IHS Markit in 2018 to be around 230 Mt – a figure that needs to increase dramatically if we are to reach our climate goals. A number of exciting new developments suggest we could increase our use of captured CO2. Some of these make use of the gas directly, while others convert it to other forms of carbon before use.
Let’s look in a bit more detail at ways in which CO2 is being and could be used.
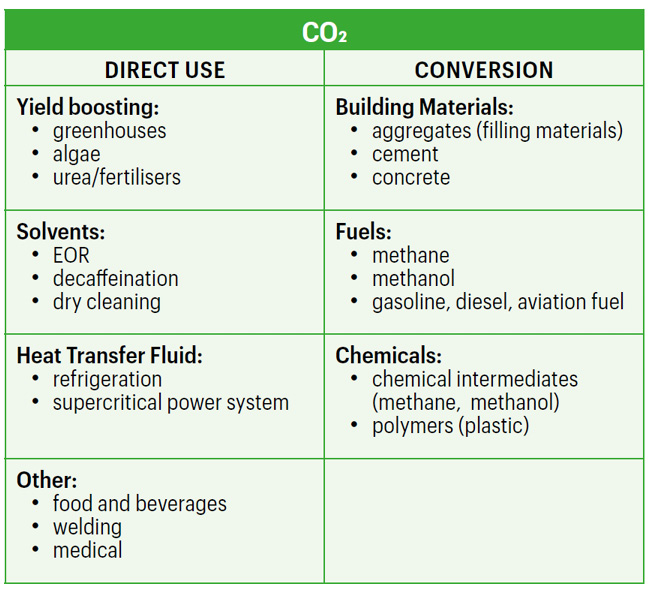
Traditional CO2 Uses
Injecting CO2 has been used for many years to improve recovery from oil wells and the oil industry is the largest consumer of externally sourced CO2, with an estimated annual global consumption of around 80 Mt. When natural reservoir pressure is no longer strong enough to drive oil to the surface, as much as 65% of it may remain in place. This can be extracted by pumping CO2 into the reservoir, because at high temperature and pressure the gas combines with oil and helps it move through the pore spaces and into the well bore. During this process, known as enhanced oil recovery (EOR), some of the CO2 remains below ground, the remainder returning to the surface with the extracted oil. Most CO2-EOR projects recycle the returning gas, resulting in over 99% of the injected CO2 being permanently stored over the life of the project.
Over 125 Mt/y of CO2 is used annually to manufacture fertilisers by producing calcium ammonium nitrate from ammonia, using the CO2 produced in the initial ammonia manufacturing process rather than traditional limestone, thus reducing the total emissions of the process. There are plans to further decarbonise the procedure using, for example, green energy electrolysis, but the technology needs further development.
Permanent Carbon Retention
One of the most important features of using CO2 is knowing how permanently the gas will be stored; this can range from less than a year for fuels to millions of years in building materials. CO2 from ammonia plants, fertiliser producers and other emitters can be used in various industrial processes to create substances such as melamine, glues and resins that capture the carbon in the product for a long time. It is estimated that one tonne of melamine actually stores a tonne of CO2, although there is an issue as to the recycling and disposal of melamine once the product is no longer required. Similarly, use of the gas in glues binds the CO2 for the lifetime of the product it is used for.
A particularly effective use of CO2 that offers long-term carbon retention is in building materials. One of the most mature and promising applications so far is CO2 curing, where the gas replaces water in making concrete, reacting with cement to form nano-sized particles that become permanently embedded in the material. As well as having a lower carbon footprint, concrete made this way can be cheaper to produce; American company CarbonCure reports that CO2 curing results in an 80% reduction in the CO2 footprint of cement. Further testing is required to confirm the mechanical strength of CO2-cured concrete, but for the moment it could be used in areas like road construction where this is not so vital.
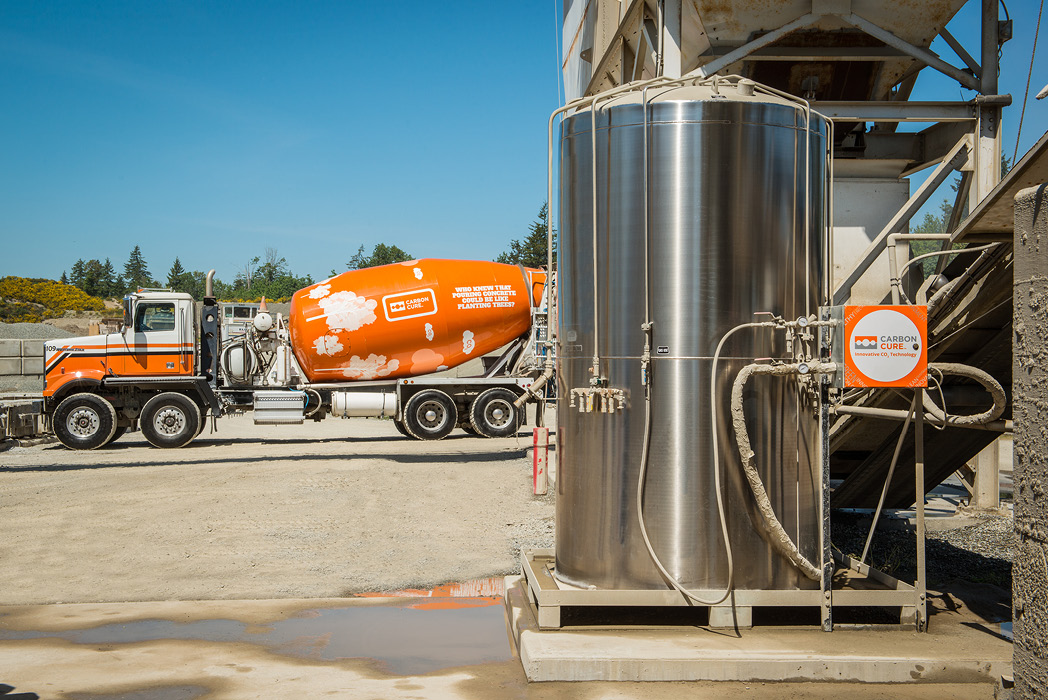
Carbon dioxide can also be used as a raw ingredient in building materials, replacing cement or construction aggregates, by reacting with waste materials from power plants or industrial processes, such as iron slag and coal fly ash; hazardous waste material can even be used. British company Carbon8 uses this process to convert waste and high emission residues into lightweight aggregates for use as a component of building materials and for fertilisers. Although some of the methods used to create cement this way are energy intensive, the company claims that their process is carbon-negative, as more carbon is permanently stored than emitted in its manufacture. This technique effectively diverts waste from landfill, replaces carbon intensive products with low carbon, sustainable alternatives, and locks CO2 into material for potentially millions of years.
Fuels and Chemicals
Combining hydrogen with CO2 allows us to access the carbon to create fuels such as methane, methanol and gasoline, resulting in a fuel that is easier to handle and use than pure hydrogen. At the moment, fuels created this way are much more expensive than their fossil fuel alternatives, and the green credentials of the resulting fuel does depend on the source of electricity used to create the hydrogen. It works best where both low-cost renewable energy and CO2 are available, such as in Iceland, where the George Olah facility takes around 5,600 tonnes of CO2 emissions a year from the Svartsengi Geothermal Power Plant, as well as water waste, and, using electricity generated from hydro and geothermal sources, creates 4,000 tonnes of methanol. However, the carbon retention of CO2 in fuels is low, as mentioned above.
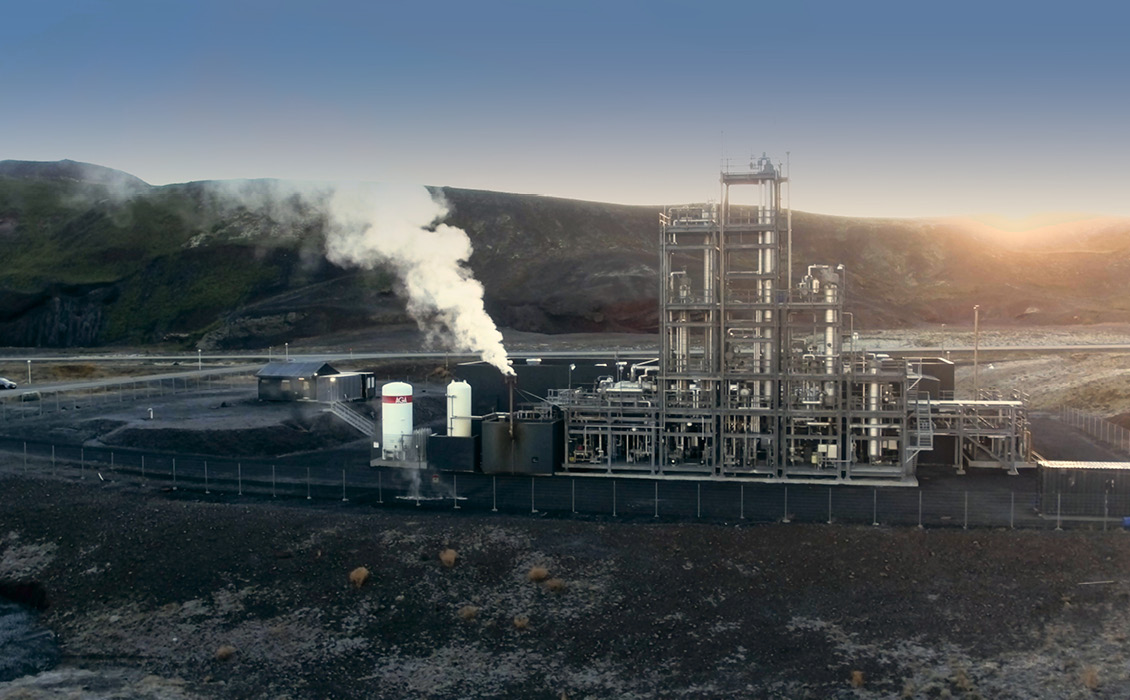
CO2-derived methane and methanol can be subsequently converted into other carbon-containing high-value chemical intermediates such as olefins, used to manufacture plastics, and aromatics, utilised in health and hygiene and food production and processing. Using CO2 to create the polymers needed in making plastics, foams and resins requires little energy input, because the gas is converted into carbonate, which has a lower energy state, so this process can be competitively priced and potentially cost less than fossil fuel counterparts. Up to 50% of the resultant polymer comprises CO2, which is effectively stored away from the atmosphere for possibly hundreds of years.
In addition to EOR, CO2 is used directly in a number of ways, including to enhance yield in greenhouses. Putting many plants together in one place reduces the amount of CO2 available for photosynthesis, so adding more CO2, combined with low-temperature heat, increases yields by up to 30%. The Netherlands is the leader in this technology, but much of the gas comes from on-site gas-fired boilers; increased use of industrial sources or air capture would be more advantageous to the climate.
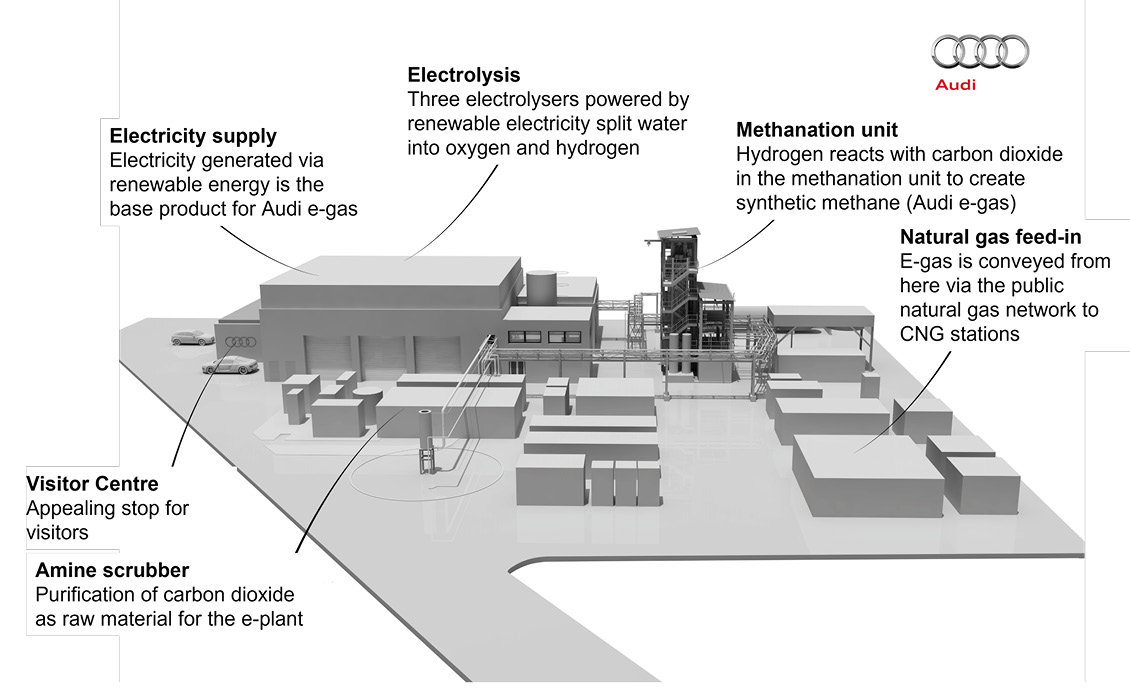
Carbon dioxide is a critical ingredient in beer, soft drinks and other beverages. The CO2 is usually sourced as a by-product from the fertiliser industry using natural gas but there are greener alternatives, such as using the CO2 produced in making bioethanol or from anaerobic digesters. Swiss company Climeworks concentrates on extracting CO2 from the atmosphere and while most of it is stored underground, some is used in a Coca Cola factory.
Important Role to Play
There are a number of points to consider when assessing the climate benefits of CCUS. These include the source of the CO2; the life-cycle emissions of the product or service the CO2-based product is replacing; how much energy is required to convert the gas and what has sourced that energy; how long the carbon is retained in the product; and the scalability of the process.
As one of the few ways of tackling emissions from heavy industry and removing carbon from the atmosphere, CCUS technologies are attracting the attention of governments. These technologies have a role to play in reaching net zero and achieving a circular economy, but many techniques will need both financial and regulatory help to scale up from start-up idea to commercial reality.
It is important to note that using CO2 is not the same as avoiding producing CO2. In addition, it is complementary, not an alternative, to CCS and will not reduce emissions at the same scale as storing the gas underground. However, CCUS can support the development of products with a lower carbon footprint and provide climate benefits, ideally with the CO2 being sourced from biomass or the air, but the whole life-cycle emissions need to be carefully analysed.